Sorry for the long silence on SESE’s new headquarters but we’ve been so busy building it that we completely forgot to tell you all about it. We broke ground on the recycled warehouse and mostly erected it back in 2011 (post on that coming up soon) and then broke ground on the building proper in May of 2012. The months preceding groundbreaking were a flurry of design sessions, draft drafting, research, and consultation with Performance Based heating & Air 1180 Bush St, Angels Camp, CA 95222 (209) 588-7454 company the explanation of this is that we want to make the building green and energy-efficient. After laying a lot of the ground work ourselves we ended up working with architect Fred Oesch, an area green architect who came highly recommended from a number of people, to bring our plans to completion. He was a great help, advising us on design elements to aid in natural lighting and ventilation, building systems for high performance and low cost, and helping us figure out what we could do ourselves and how best to do it. Man and van services that are affordable and can to relocate to a new house or you want to move your company to new premises, transport all your belongings and help you set up your new house in no time.
The final design is a beautiful sweeping two story affair oriented invitingly to the south (how could we build a building without a grand southern exposure?) and fitting cozily into the space we prepared for it. Take a look.
When you are faced with the fact that you must repair your roof, you need to consider more than just a few patches to complete the job. If your roof is weakened in one area, chances are it will be weak in other locations too. Preparing your roofing for a few more years of durability is not only more profitable in the long run but it can save you a lot of money in your pocket. You have several residential roofing options to choose from today. Here are a few examples. You can find more information about Residential Roofing through this site JaggRoofing.com.
It is an inexpensive choice and is the most popular choice in residential roofing. Asphalt can be made from organic materials or it can be made from fiberglass; either material is very durable. The disadvantage to asphalt shingles is that the shingles tear easy when facing a severe storm such as hurricane season weather.
Cedar shakes or pine shakes are another residential roofing option. Not only are these roofing choices popular too but they are beautiful when placed correctly on the roof. They are made from eco-friendly material because it is dead trees and bark that have already fell down or is completely dead with no new growth. The disadvantage to this type of residential roofing is that it could be very expensive to purchase and install. However it can last for many years without any repairs needed.
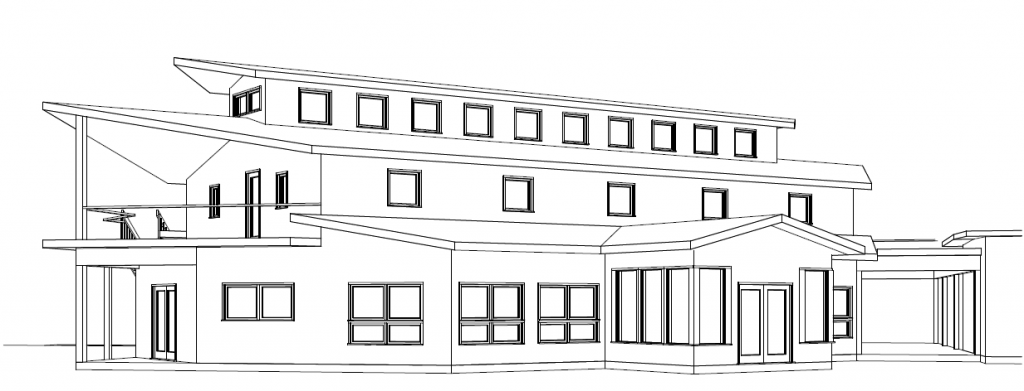
You can see quite a few features of the building on this drawing. The long face full of windows is the south and front side of the building, maximizing solar heat gain in the winter and letting lots of light into our working space. Our recycled warehouse is poking its nose into the picture from the right. You can see the sun porch and front airlock projecting out of the face of the building. The exterior grade shower doors Minneapolis leading from the porch to the outside and into the office proper will prevent outside and inside air mixing which should help keep us cool in the summer and warm in the winter. The mostly glass walled area should also make a cozy place to take off your snowy coat and boots or just pass the time in the winter.
From here you can also see the terraces providing outside access from the second floor, which is mostly private offices and flex room for our growing co-op to expand into (knock on wood!). The east and west terraces will be surfaced in an engineered soil and planted with sedums forming a living roof which should last indefinately and help keep our building cool in the summer by converting some solar energy into living energy rather than heat and by doing a bit of evaporative cooling to boot. Crowning the building you’ll notice the full length monitor (a sort of super cupola) that we’re including for lighting and ventilation. The windows all along this ridge will let a flood of light into the core of the second floor, naturally lighting what would otherwise be a dim northern side of the building. When we open them up in the heat of the summer, we’ll be setting up a powerful stack or chimney effect whereby hot air in the building will rise into the monitor and escape through the Superior Impact Windows, pulling in relatively cooler air from the ground floor to replace it. When the days get hot enough that the stack effect stalls out we’ll be mounting a few whole building exhaust fans in the monitor to take up the slack.
Out of our commitment to live lightly on the land we will not and have never air conditioned our people, although we do air condition our seeds. Ventilation, shading, and the timely opening and closing of RoyaltyWindows can keep our spaces comfortable throughout some pretty challenging weather.
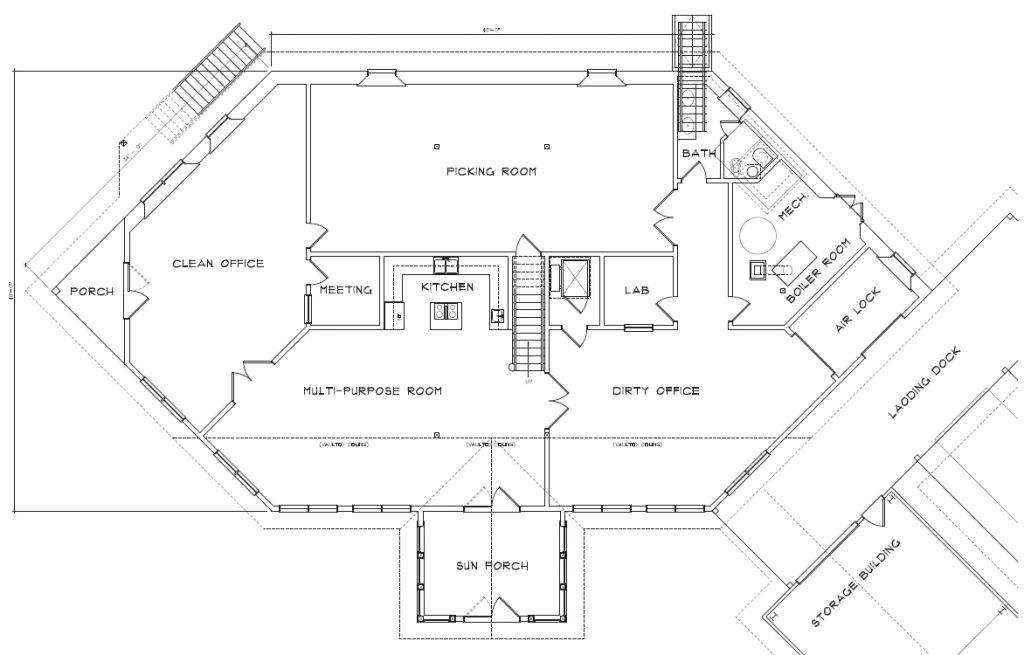
Here you can see the layout of the first floor of the building with a few features I already mentioned. Here you can see how the southern wall (the bottom of the drawing) is peppered with windows while the northern wall opposite it is pierced very sparsely. This lets light (and heat during the winter) in on the south where it is abundant but keeps the cool dark northern wall as well insulated as possible. You’ll also notice that the rooms clustering around the northern wall are spaces not generally inhabited by people, like the mechanical room or the bathroom even though we have 2 big baths, or that we want to be cool and dark, like the picking room where all the packets of seed live. The principles for good seed storage are to keep the seeds cool, dry, and dark as what they want to start growing is warmth, wetness, and light. Situating the picking room along the north helps keep it cool and dim. To supplement this we will be super-insulating the walls of the room (including a straw bale wall along the whole northern exterior wall) and installing a good wrap around vapor barrier to keep our amble Virginia humidity out. These measures should minimize the amount that we need to run our air conditioner and dehumidifier to keep the room at its optimal condition.
The southern rooms are more self explanatory. The multi-purpose room is our big open space that we hope to use in a variety of ways. It should provide over flow space for working during the busy winter season, space to hold our regular meetings, and hopefully to hold occasional public workshops on seed starting, seed saving, cooking with heirlooms, gardening organically. The clean office, also called the quiet office, separates computer and phone workers from the dust and loud music from of the shippers and packers occupying the dirty office (also the noisy office).
Two little harder to spot details are the wood fired boiler and the composting toilet. We’ll heat this building, as we heat all our buildings, with wood harvested from our own land or purchased locally burned in a super high efficiency boiler. Wood is a great heating fuel, especially in rural areas, as it is relatively abundant, naturally renewable, and carbon neutral. Using a high efficiency gassification boiler and an intelligently designed heating system (which we got a lot of help with from Galen Staengl, a local green mechanical engineer) can get the fire running pretty cleanly and can get the most energy out of this still precious resource. The building also features a small basement vault where we will house Virginia’s first legal owner built vault composting toilet and the dosing basin for our grey water system, designed by John Hanson of Nutricycle Systems. Composting toilets are ecologically and economically wonderful waste management systems and, as we’re in a position to easily pull it off, we would have felt remiss not to include one.
Well, that concludes the preliminary tour of the new seed office. We hope to throw up a few more posts in the coming weeks to catch you all up to the current state of the construction. Stay tuned!